What is Porosity in Welding: Necessary Tips for Achieving Flawless Welds
What is Porosity in Welding: Necessary Tips for Achieving Flawless Welds
Blog Article
The Scientific Research Behind Porosity: A Comprehensive Guide for Welders and Fabricators
Understanding the detailed devices behind porosity in welding is essential for welders and fabricators striving for remarkable craftsmanship. From the structure of the base materials to the ins and outs of the welding process itself, a wide variety of variables conspire to either worsen or reduce the presence of porosity.
Comprehending Porosity in Welding
FIRST SENTENCE:
Exam of porosity in welding discloses vital understandings into the honesty and top quality of the weld joint. Porosity, identified by the visibility of dental caries or gaps within the weld metal, is a common problem in welding procedures. These gaps, otherwise effectively resolved, can compromise the structural honesty and mechanical residential properties of the weld, bring about potential failings in the ended up product.
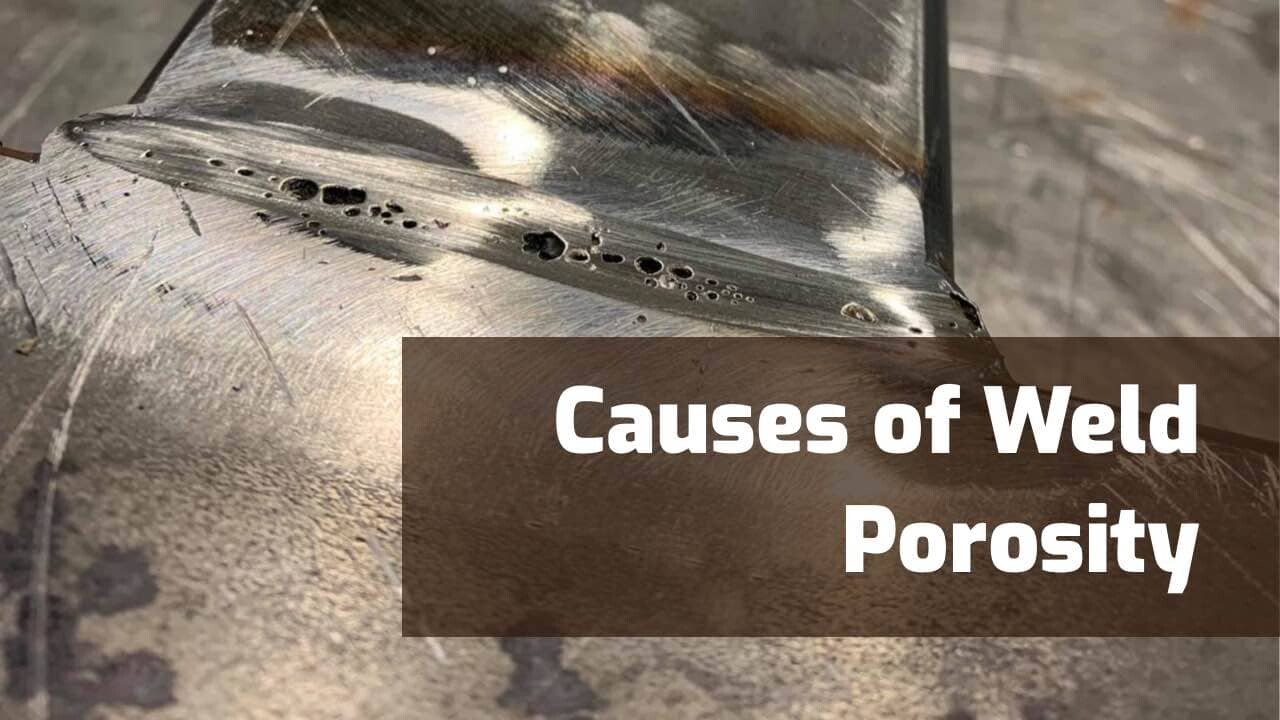
To find and evaluate porosity, non-destructive screening approaches such as ultrasonic screening or X-ray inspection are frequently used. These techniques allow for the recognition of internal problems without endangering the integrity of the weld. By evaluating the size, form, and distribution of porosity within a weld, welders can make informed decisions to improve their welding processes and achieve sounder weld joints.

Elements Influencing Porosity Formation
The incident of porosity in welding is affected by a myriad of factors, varying from gas securing effectiveness to the intricacies of welding criterion setups. Welding parameters, consisting of voltage, current, take a trip rate, and electrode type, additionally influence porosity development. The welding method used, such as gas steel arc welding (GMAW) or shielded metal arc welding (SMAW), can influence porosity development due to variants in heat distribution and gas coverage - What is Porosity.
Impacts of Porosity on Weld Top Quality
The visibility of porosity additionally deteriorates the weld's resistance to deterioration, as the entraped air or gases within the gaps can respond with the surrounding atmosphere, leading to degradation over time. Furthermore, porosity can prevent the weld's capacity to endure stress or effect, further jeopardizing the total high quality and reliability of the welded structure. In important applications such as aerospace, automobile, or structural building and constructions, where security and sturdiness are vital, the damaging impacts of porosity on weld quality can have serious consequences, emphasizing the relevance of lessening porosity through correct welding techniques and treatments.
Strategies to Reduce Porosity
To boost the high quality of bonded joints and ensure architectural stability, welders and fabricators utilize certain methods intended at reducing the formation of voids and cavities within the material during the welding process. One reliable method to reduce porosity is to ensure appropriate product prep work. This includes detailed cleaning of the base metal to remove any type of contaminants such as oil, grease, or wetness that could add to porosity formation. Furthermore, making use of the suitable welding specifications, such as the right voltage, existing, and take a trip rate, is essential in preventing porosity. Maintaining a consistent arc size and angle throughout welding also aids decrease the probability of porosity.

Making use of the proper welding strategy, such as back-stepping or employing a weaving motion, can likewise help disperse warm evenly and lower the chances of porosity development. By carrying out these strategies, welders can effectively decrease porosity and his explanation create high-grade welded joints.
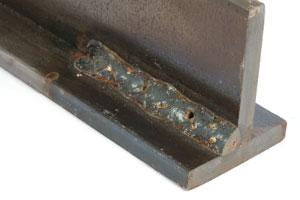
Advanced Solutions for Porosity Control
Carrying out innovative technologies and ingenious methods plays a critical role in achieving remarkable control over porosity in welding processes. Furthermore, employing sophisticated welding strategies such as pulsed MIG welding or changed ambience welding can likewise help have a peek at this website alleviate porosity issues.
One more advanced remedy entails the usage of innovative welding tools. For circumstances, utilizing devices with integrated features like waveform control and advanced source of power can improve weld top quality and lower porosity risks. Moreover, the implementation of automated welding systems with accurate control over criteria can substantially minimize porosity problems.
Moreover, integrating advanced surveillance and assessment modern technologies such as real-time X-ray imaging or automated ultrasonic screening can aid in finding porosity early in the welding process, permitting for prompt rehabilitative activities. On the whole, integrating these advanced remedies can greatly boost porosity control and enhance the overall high quality of bonded elements.
Verdict
In final thought, comprehending the scientific research click here to read behind porosity in welding is necessary for welders and makers to produce top quality welds - What is Porosity. Advanced solutions for porosity control can further enhance the welding procedure and make certain a strong and reliable weld.
Report this page